Interview: Blackwood Engineering’s evolution
26 August 2021
Lindsey Anderson speaks with Blackwood Engineering’s Sales Director Dominic Connor about the company’s history, growth and future.
Blackwood Engineering, founded in 1946, is a supplier of castings and counterweights for access equipment and telehandlers. A family business with a proud history in the casting industry, Blackwood Engineering has grown substantially over the past half century from its humble beginnings as a UK-based general foundry.
Blackwood diversified in the 1970s, and expanded its product range to begin producing counterweight castings that it would focus on for the next two decades. When the 1990s rolled up the company broadened its range again, introducing ductile iron and steel while also starting to focus on more complex engineered castings.
Under the ownership of Paul Connor since 1994, Blackwood Engineering is now a global enterprise with operations and warehousing facilities located in Belgium and South Wales. They also work with facilities in both China and India.
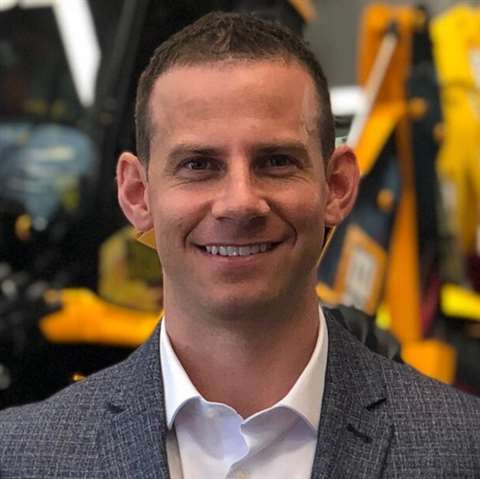
Dominic Connor, sales director with Blackwood Engineering, said, “The company was quick to recognize the emergence of China as the most competitive place to source casting products. The company has been producing castings with our Chinese foundries since 1997.”
Blackwood made another major shift in 2002, when it decided to close down its own in-house foundry and transfer all production to China. Growth beckoned again and so Blackwood expanded by openinged a facility in India in 2015.
Connor explained, “We are increasing our production in India to support our growth as India offers a viable, long-term alternative-manufacturing option. Unfortunately, it became unviable to continue our UK foundry a long time ago.”
Blackwood Engineering’s castings and counterweights are primarily a range of iron and steel material grades. The company is a leading provider of castings and counterweights to global manufacturers of construction equipment, access platforms and industrial forklifts.
Connor added, “We work with some of the leading manufacturers in the industry and have done for several decades. They chose Blackwood because at the time we were a foundry in the UK, so they respect our longstanding heritage in the industry.”
Access, Lift & Handlers editor Lindsey Anderson recently quizzed Connor to dig deeper into the company’s counterweight designs and manufacturing processes, industry trends and the market as a whole.
What services do you provide?
Dominic Connor: Aside from providing the product itself, our main value added service to our customers is the level of safety stock that we hold for them at our sites in Belgium and the UK. This allows us to meet short-term demand changes so that our customers can capitalize on short notice order changes from their customers.
Our main internal production process is our gloss painting, and we have recently invested further into our gloss painting facilities in Belgium and the UK.
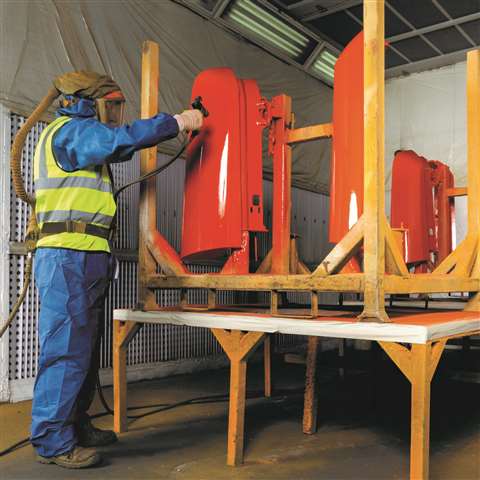
How have counterweights evolved?
DC: Counterweights have become a lot more complex over the years and now involve more intricate styling to reflect the modern look of the machines that OEMs produce.
The counterweight function has evolved from being a basic ballast to now being an important part of the chassis and overall machine model.
Are OEMs seeking out new counterweight designs or requirements?
DC: Yes, our customers are constantly looking for ways to improve machines, from both a performance and aesthetic standpoint.
The newer counterweights often have more machining, often requiring CNC, to meet the tighter tolerances. The greater demand for compact machines continues to change the requirements of the counterweights.
As well as the ever-evolving outer shape designs, this also impacts the inside facing parts of the counterweights that mate with many internal parts of the machine.
What trends are you seeing in the marketplace right now?
DC: As with other markets, customers are launching more and more electric and hybrid models. We are also seeing strong demand for compact telehandlers.
Customers are also looking deeper into their existing machines and carrying out our Value Analysis/Value Engineering exercises to optimize the design-to-cost element.
How did the global pandemic affect business? How do you see the next 12 months panning out for Blackwood?
DC: There was of course a very challenging period in the early days of the COVID-19 pandemic as orders came to a standstill for a couple of months. But thankfully, since the fourth quarter of 2020, the demand has bounced back well and has since been much stronger than anticipated.
Going forward, the market demand looks to be very strong and next year is projected to see further increases so it is positive news and there are lots of new projects to be excited about.
The main challenges we have faced this year such as unprecedented shipping costs and congestion, will continue for the foreseeable future. Rising commodity costs this year have also driven up the cost of our products, and we are working hard to manage this as best we can.
Despite the challenges, we continue to invest in our business from a facilities and people perspective as we continue to build for the future.
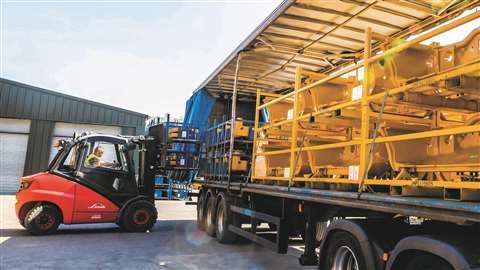