A material improvement for heat exchangers
14 April 2022
Using aluminum to make heat exchangers isn’t a new idea – think of your car’s radiator. But aluminum hasn’t made significant inroads in larger engine applications, mostly because of worries about the material’s robustness.
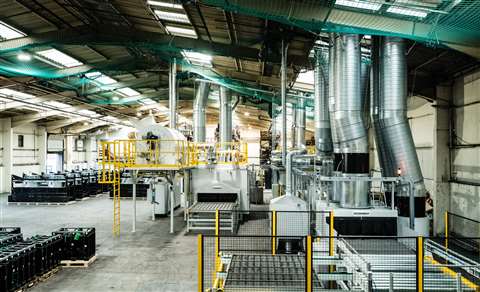
Now Wabtec thinks the time is right to make a big bet on aluminum’s future across multiple market segments.
The company is investing $8 million to install two furnaces that will produce aluminum-based heat exchangers for applications that traditionally use copper brass designs, said Mike Fetsko, president of the Freight and Industrial Components Group for Wabtec.
“We know that this is going to be a more cost-effective solution for our customers,” said Michael Sprenger, director of sales, Engine Cooling for Wabtec. “The copper brass is working, it’s very scalable, we can satisfy all the requirements worldwide, but we do know this (aluminum) is going to be a lower cost point for our customers to make them more competitive.”
Heat exchangers for demanding applications
The two furnaces will produce two types of heat exchangers for large engines that go into demanding applications, such as mining, oil & gas and rail.
One furnace is currently being installed at the company’s Northampton, UK, facility. That operation already designs and manufactures a variety of cooling systems and related components, including radiators and charge-air coolers. The Northampton site is one of the largest producers of industrial radiators in the world, manufacturing over 35,000 radiators a year for companies in the power generation, off-highway and construction industries worldwide.
At the company’s facility in Jackson, Tenn., an additional bar and plate furnace will be installed this year to enable the company to produce what it calls the largest single-piece aluminum core in the market. The product will be well suited for mining, oil & gas, rail and the marine auxiliary markets.
The new Northampton, UK, tube and fin furnace will produce sectional heat exchangers – “think Lego blocks,” Sprenger said – that will be more suited for stationary markets.
“With those two technologies, we’re trying to cover all of those market segments,” Sprenger said. “They are two technologies, but with the both of them we feel we can cover the gamut.”
Sprenger said the difference in the two types of heat exchangers has much to do with the geometry of the core. The bar and plate process uses a heavier gauge of aluminum and the sectional design in the UK is tube and fin, so that would look more conventional is terms of seeing individual tubes and individual fins. There are different geometries of heat transfer surfaces as well, which Sprenger declined to delve too deeply into.
“That’s part of the intellectual property, the secret sauce that we’ve been working on and developing internally to optimize the heat transfer surfaces to get the cooling we need in the applications we need,” Sprenger said.
The benefits of aluminum in radiators
In the early 1980s, copper brass made about 95% of the radiator market for passenger vehicles in North America. Since then, mostly to satisfy environmental considerations and to improve fuel efficiency through weight savings, aluminum has become the go-to material for radiators and other components including heater cores, condensers and evaporators.
But for heavy-duty applications, aluminum was often considered too delicate. Yet aluminum does have advantages, Fetsko said, noting it’s less expensive than copper brass designs and can be more easily recycled.
“Overall they’re more eco-friendly,” he said. “That’s not to say we’re going to discontinue our copper brass technology, it just allows us to be more well-rounded, to offer a better product suite – basically whatever our customers want.”
Sprenger, who’s been in the industry for more than 30 years, said there’s been a trend toward higher power nodes across nearly all markets and applications.
“What we’re seeing in the marketplace – where our solution is going to be good for our customers – is the power outputs for these diesel and gas engines continue to go up in terms of horsepower output,” he said. “Twenty, 30 years ago, a big power node was 2 MW – now it’s 4. We’re bringing this aluminum technology to market to handle these higher outputs and at the same time getting a more cost-effective solution for our customers.”
Investment in aluminum technology
Wabtec sees the investment in aluminum technology enabling the company to grow into other market segments as well, Fetsko said. While the first market for the technology will be the higher power nodes, the technology can be branched out.
“We’re really able to capture a segment of the market that copper brass probably can’t, cost-effectively,” Fetsko said. “So we see ourselves as able to handle the highest outputs as well as now successfully a market to smaller power modes, so we see this as expanding our market base as well.”
It also aligns with the company’s goal of being more of a “one-stop shop” for its customers.
Fetsko said that over the past 10 to 15 years, the company has made several acquisitions in the turbocharger market, including Napier in the UK and California’s Turbonetics. Napier focuses on turbochargers for high horsepower engines, roughly 4000 to 17,000 hp, in the marine and power generation markets. Turbonetics customizable turbochargers support engines in 100 hp to roughly 2000 hp range.
“We now have a full suite of industrial turbos as well, from much less than 1000 hp to very large applications in marine and power gen where you’re talking 15,000 hp plus,” Fetsko said. “What we’re looking to do is duplicate a strategy we’ve had in our freight car and locomotive business, where Wabtec has a full suite of products that we go in and sell to a Class 1 railroad and now we will do that same to an industrial customer.
“That goes from heat transfer equipment to turbochargers and even elastomer products – that’s where we’re really looking to grow and I think these aluminum furnaces are a huge step in that direction, it will allow us to give customers a more well-rounded product offering for any industrial application that they have.”
The company offers heat transfer solutions to a range of markets and applications. Its Unifin brand supplies products used for cooling power generation equipment, including lube oil coolers, generator hydrogen coolers and bearing oil coolers. Its Thermal Transfer brand manufactures industrial heat exchangers for niche markets such as steel. The new aluminum furnaces can be used in those applications as well, Fetsko said.
“It’s a big move for us, but we know it’s the right move and we know it’s the right move for the markets that we’re in,” Fetsko said. “I think we’re in a good spot.”