Autonomous construction
22 March 2021
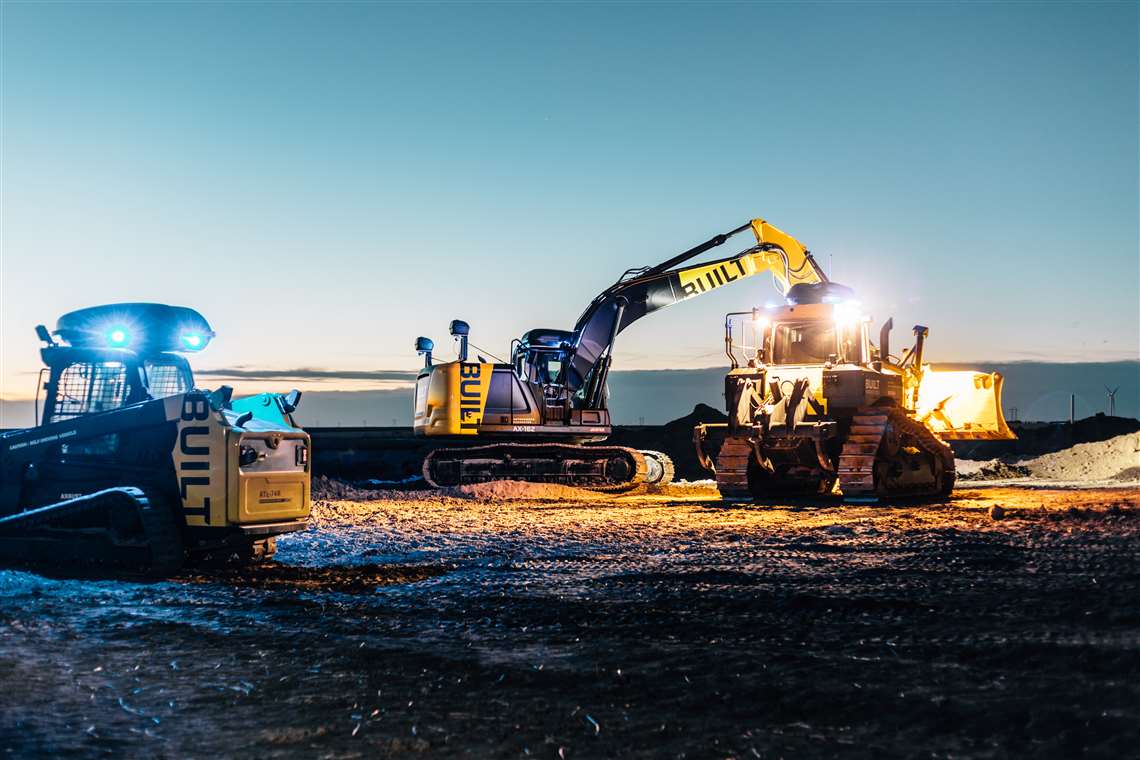
While 2020 was a year we may wish to forget, 2021 could be remembered as a year of dramatic change. In fact, if anything good can be said to have come about because of the pandemic – at least in terms of construction – it could be the industry finally waking up to the benefits of technology.
We are, for example, seeing a huge proliferation of construction technology start-ups, many of which are moving us closer to fully-autonomous machines on construction sites. This may worry some, but it shouldn’t; the primary drivers are efficiency, reduced emissions and the enhanced comfort and safety of operators.
Gaurav Kikani, vice president of the tech start-up Built Robotics, believes a different method of construction is long overdue. He says, “The way we build today is largely unchanged from the way we used to build 50 years ago. Within two years, I think we’re really going to turn the corner, and you’re going to see an explosion of robotics being used on construction sites.
“We’ll start to see technological innovation move from the mechanical side to the software side. This change will ultimately be a big win for the construction industry and help us build better, faster, and more productively to face the biggest challenges in the built world.”
Available on the market today
In this feature, we are looking at the diverse applications that can be undertaken by semi- and fully-autonomous equipment that is – more or less – available to contractors today. A straightforward example is Bauer subsidiary Rammtechnik’s (RTG) Operation Remote Control for piling rigs.
With the new tool, RTG says the entire set-up process can be carried out by an operator in just 15 minutes, with significant safety benefits, particularly on sites where space is at a premium.
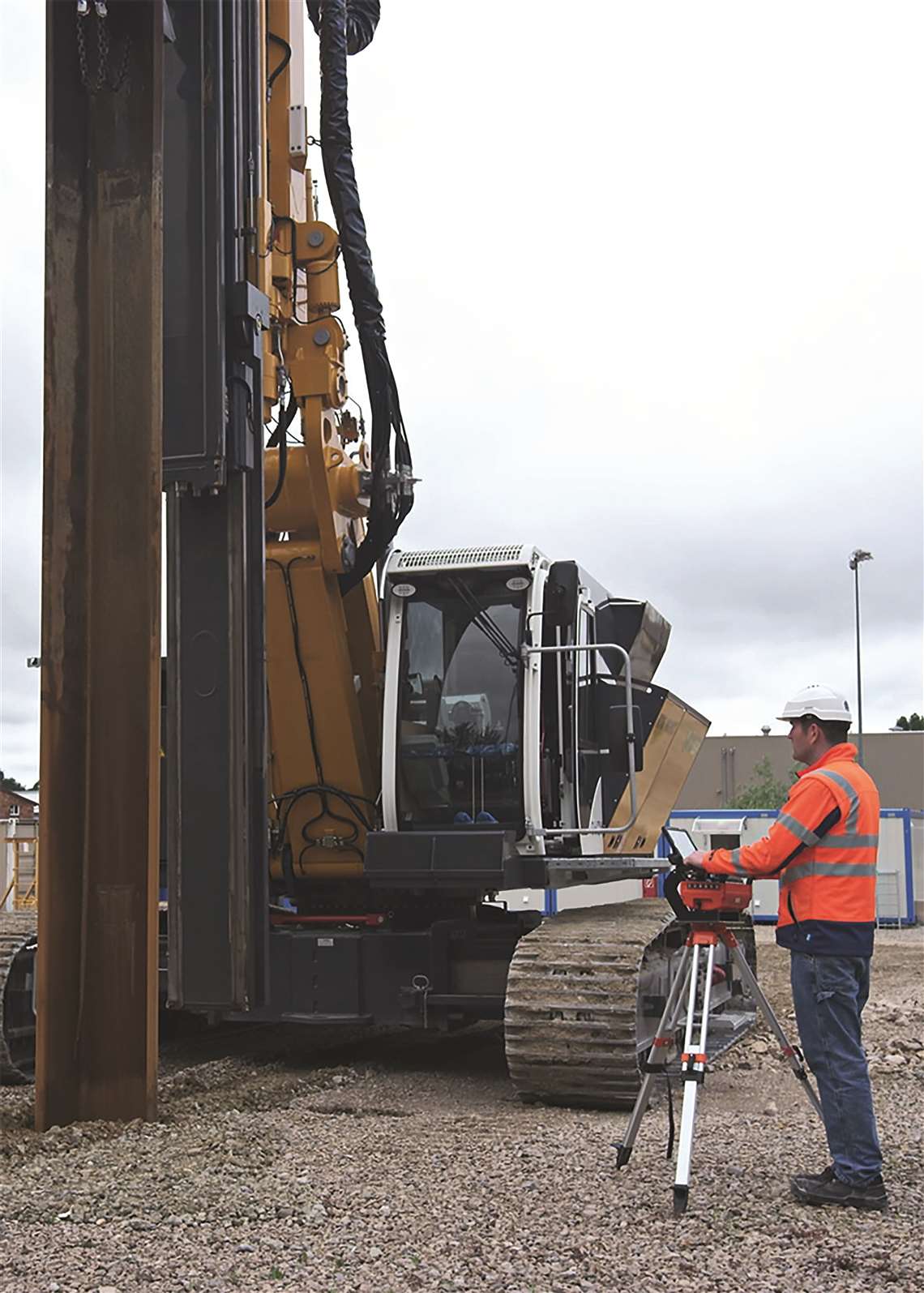
Bernhard Lindermair, RTG’s managing director, said, “The newly-developed operation remote control can be used for all applications. With the remote control, you bring the rig into position and you get all the functions for the operation on the remote-control unit.
“The machine comes with an iPad, which you remove from the cabin and put it on the remote control. So, you can see all the functions and make your reports, which is something absolutely unique for piling rigs – a big step forward in safety and, important nowadays, you can use the machine in a single-man operation.”
Moving a step further from the cab, Caterpillar recently held a press conference to announce that its Cat Command remote-control stations will be available for purchase by construction contractors in Europe from the first quarter of 2021.
Jason Ramshaw, global commercial manager for Cat Productivity – Automation & Autonomy, said the latest version of the Command solution has the potential to give operators total, almost-real-time control of their machines from anywhere in the world.
He said for employers to be able to remove their operators from potentially dangerous on-site situations was a game-changing scenario
and a first step on the road to greater autonomy in construction.
Ramshaw added that the screen quality on the latest Command stations, combined with the on-board technology – including a four-camera set-up on the machine itself – meant a remote operator could potentially enjoy a better view of the machine’s surroundings than if they were in the cab itself.
Initially available on medium excavators, from the 320 up to the 340, the technology is also expected to be available for smaller bulldozers – the D5 and D6 – by the third or fourth quarter of the year.
One customer overview, broadcast during the conference, showed the US-based civil contractor Saiia using a number of Cat Command stations in an ash field, a notoriously hazardous environment, in the country’s south-east.
The company said having a number of operators sitting together in a comfortable office trailer environment not only promoted safety but also eased operator stress, aided instruction and had led to the sharing of tips and experiences among the team.
Semi-autonomous robot
A relatively small machine that demonstrates the large strides being made towards autonomy on construction sites comes from Liechtenstein-based Hilti.
Towards the end of 2020, the OEM introduced its first robot to the market. Jaibot is a semi-autonomous mobile drilling robot, specifically engineered to drill ceiling holes. What makes the machine a little different is that it utilises building information modelling (BIM) data to accuratly locate itself within the required area before drilling.
Julia Zanona, product manager for robotics at Hilti, said, “We looked at which routine work on the construction site is among the most stressful, and that is primarily overhead work.
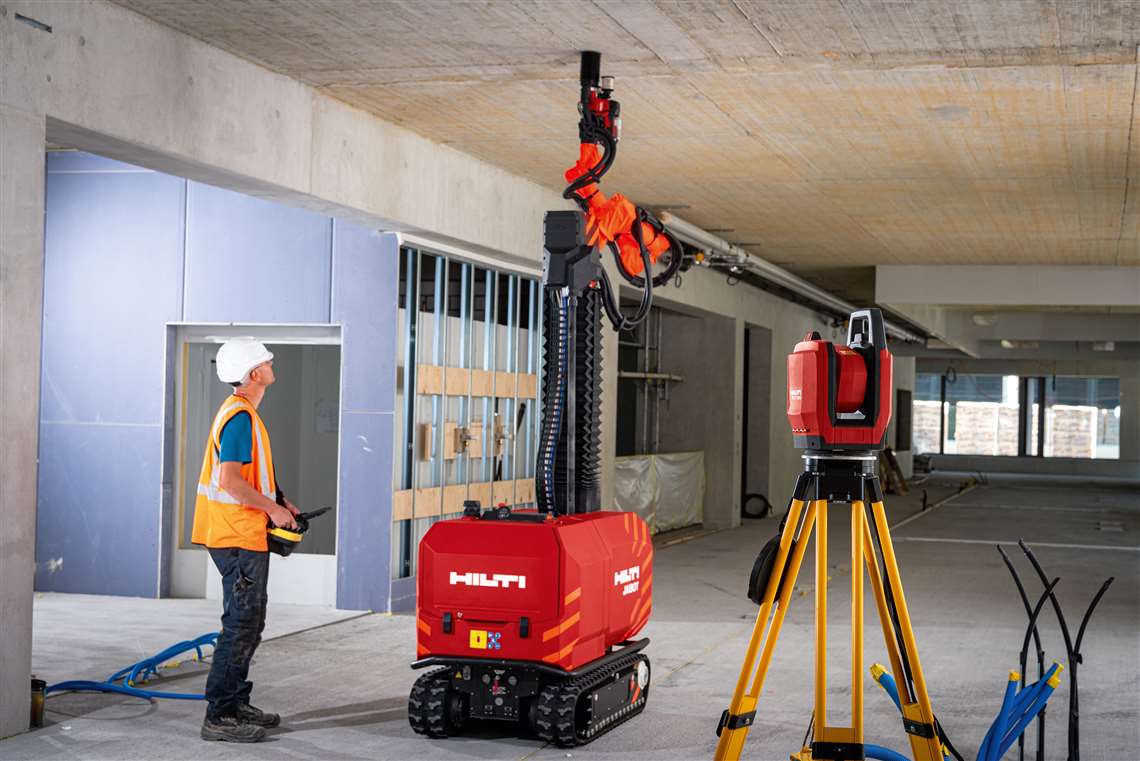
“From the beginning, it was important to us to develop a robotic solution that supports our customers where it is most needed. The Hilti Jaibot takes over the most strenuous and exhausting tasks, working alongside the installation team.”
Apart from easing the manual load and helping to reduce time and budget overruns on projects, Hilti says BIM-enabled robots such as Jaibot can make the construction process more transparent, with daily progress reports from the field sent straight to the cloud. Another benefit of this reporting is the early detection of potential conflicts between trades as a building is erected.
First unveiled at Germany’s Bauma exhibition in 2019 as a technological study, the Robomag BW154 autonomous tandem roller from German manufacturer Bomag, is another good example of the use of automation in the construction industry. Fully-autonomous equipment could change the face of road construction.
The machine’s ‘operator’ uses a laptop (or desktop) to geofence, or define an area that requires rolling. Once completed, the roller uses GPS sensors to ensure it remains within the operational perimeter and works autonomously until the entire area is compacted.
Other than loading the geofence parameters, the operator merely selects the required layer thickness; Bomag’s onboard (Asphalt Manager) technology measures material stiffness and monitors the compactive force required to achieve the desired results.
Robomag also features a handheld remote-control unit, enabling operators to take the machine beyond the geofenced area for further compaction.
While in operation, Robomag utilises four sensors to detect obstacles (including people), but also has emergency stop buttons on both sides.
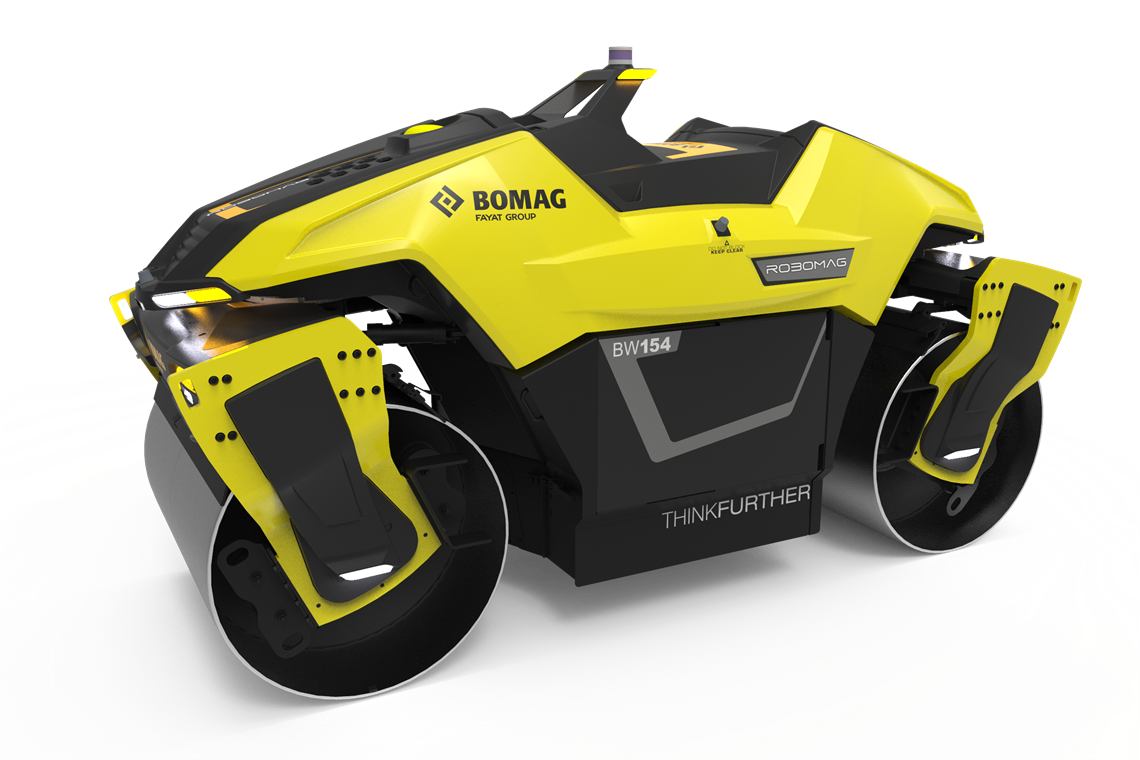
When Robomag was demonstrated at ConExpo 2020 in the US, product manager for Bomag Americas, Bert Erdman, said a great benefit of the machine was the removal of human error from the operation, with the roller making its own intelligent decisions about compaction. He added that it was the perfect option for use in hazardous areas such as mining tunnels.
Software is the key
When Built Robotics’ Gaurav Kikani joined one of our recent Construction Technology webinars on the subject of autonomy, he said, “The critical element for taking the next big leap for construction is really going to be on the software side – that’s where the core technology behind automation exists.”
The company was launched five years to develop an upgrade system for already-existing equipment. This system basically turns standard equipment into fully-autonomous construction machines.
When Kikani talks about full autonomy, he refers to what is known as level 4 autonomy, which means there is no operator inside the cab. At this level, a machine can receive commands for its operation and carry them out with no supervision.
As the system rolls out – and Built’s robots are, according to the company, already deployed across the industry – Kikani believes we are seeing a, “paradigm shift” in construction and calls the new technology “the biggest thing since hydraulics.”
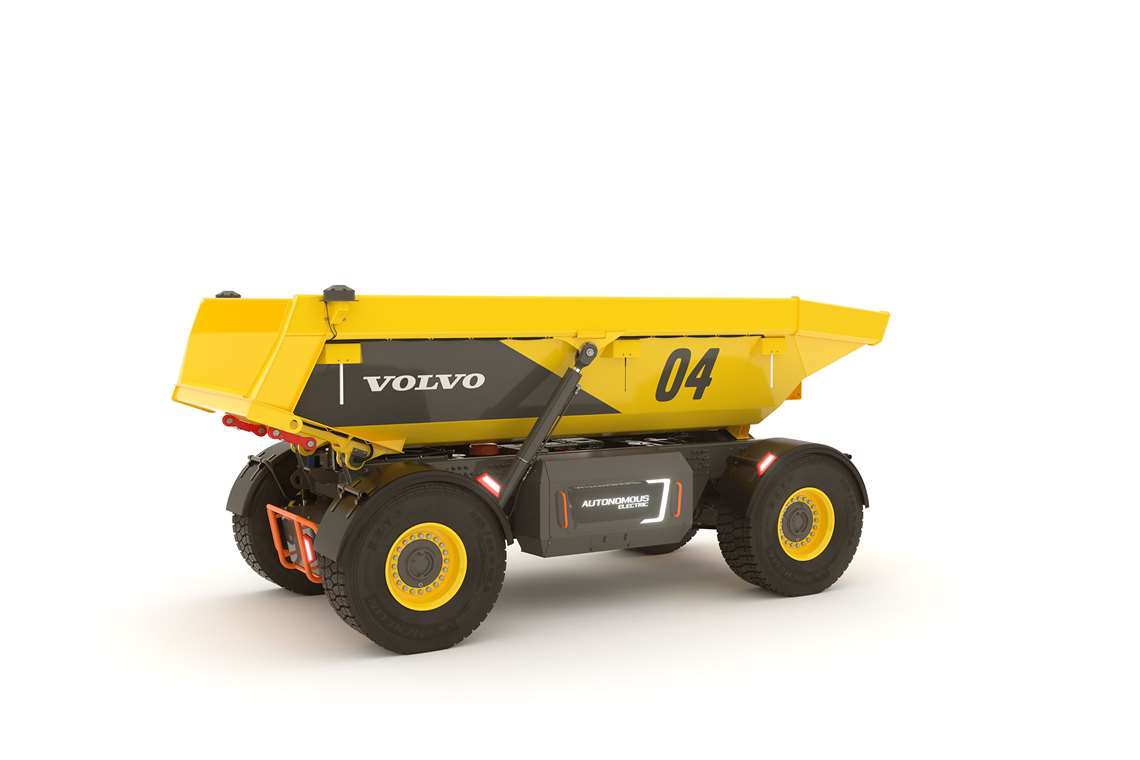
Nils Jaeger, president of Volvo Autonomous Solutions (VAS), has a similar philosophy. He says, “I’m absolutely convinced that autonomous solutions are beneficial to society. This new industry will provide a lot of value – safety, efficiency, flexibility, sustainability and economic.
“It is impossible to stop progress – this technology is going to happen – and I firmly believe that it will be a force for good. In fact, if we had been further ahead in our development, the impact of Covid-19 would have been less.”
Jaeger has responsibility for developing autonomous systems for on-highway and off-highway vehicles, but says there are still many hurdles to overcome in terms of road vehicles. With off-highway, he believes the technology is mature enough to offer credible alternatives today.
Perjohan Rosdahl, head of Off-Road at VAS, says, “Our approach is to start small, in a tightly confined environment and build on our successes over time. A perfect place to start is quarries, which have clearly defined load-and-dump locations over generally short circuits.”
Quarries tend to have carefully mapped out safety plans, and VAS says there is no need for regulatory changes when placing autonomous machines in these environments.
Working closely with Volvo Construction Equipment, VAS says its new machines, whether developed specifically to be autonomous – like the TA-15 hauler – or traditional operator-based equipment, use the same autonomous drive platforms, coding languages and so on. This allows them to be ‘talked to’ in the same way, as well as offering the ability to scale up easily.
In this way, while not all machines will be autonomous, they will be ‘autonomous enabled’, allowing VAS to ‘upgrade’ standard products into operator-less machines, using its own proprietary autonomous drive kit.
Tasks such as site scans, surveying and progress monitoring are both repetitive and, from a technological perspective, straightforward.
This is one area where most laymen could imagine a piece of autonomous equipment taking on the task. Few, however, would picture the solution dreamed up by Boston Dynamics, or understand the sophisticated technology either within it or carried by it.
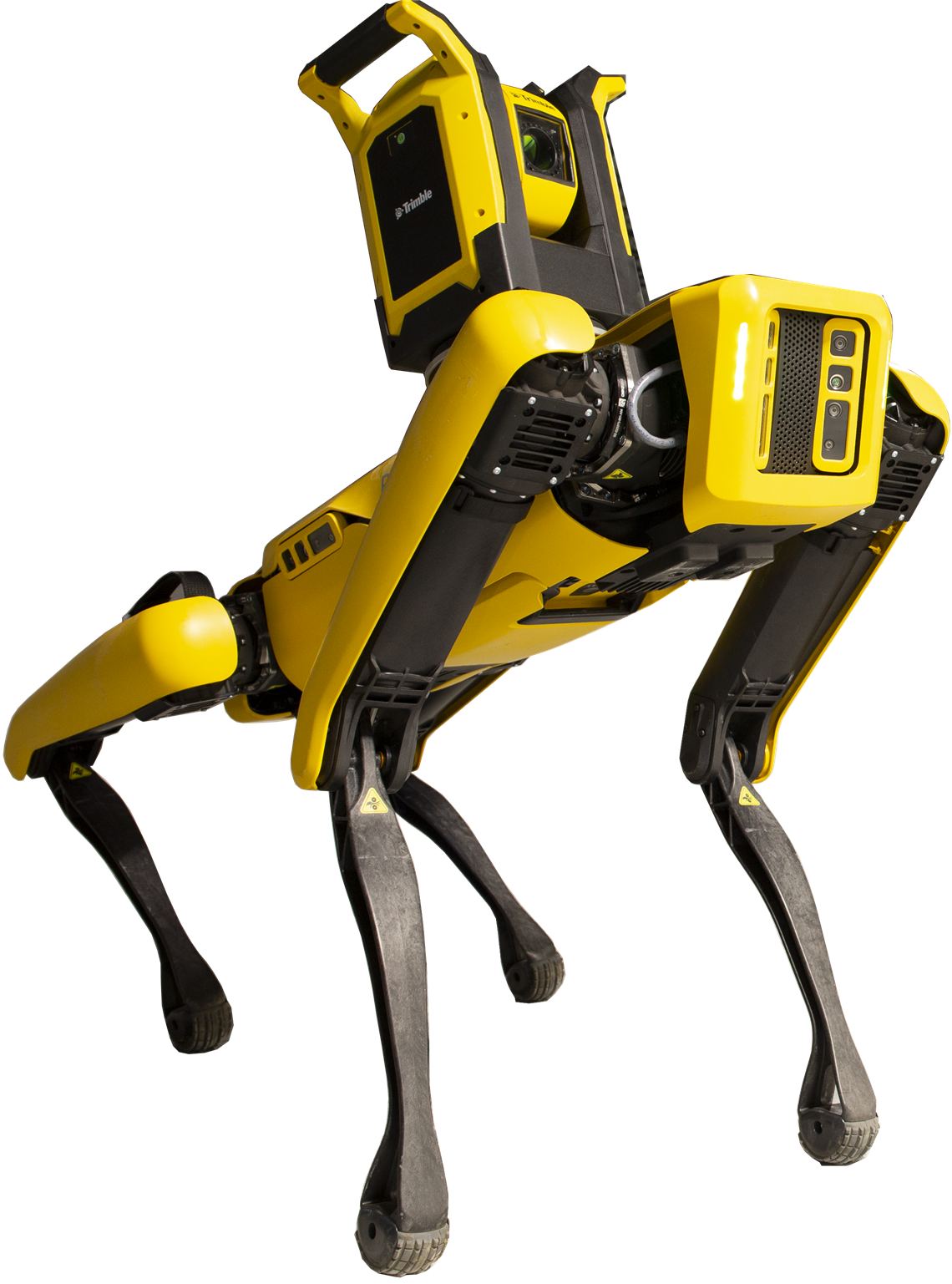
Spot, is an incredibly complex robot platform, which has cutting edge technology built into its four-legged movement. The machine’s mobility allows it to travel almost anywhere on a construction site, including up and down stairs and over soft, uneven ground, while carrying an array of scanning and data-collection software on its back.
In October last year, Boston Dynamics formed a strategic alliance with software giant Trimble, allowing Trimble to sell and support Spot with integrated scanning, total station and GNSS technologies for the construction market.
Michael Perry, vice president of business development at Boston Dynamics, said of the deal, “The integrated solution will enable any jobsite leader to deploy Spot and Trimble technologies to get an accurate view of construction progress through real-time data collection. With a more comprehensive view of site activity, project managers can take proactive measures to ensure on-time, on-budget and safer project delivery.”