British Steel invests £26m to meet rising equipment demand
08 September 2021
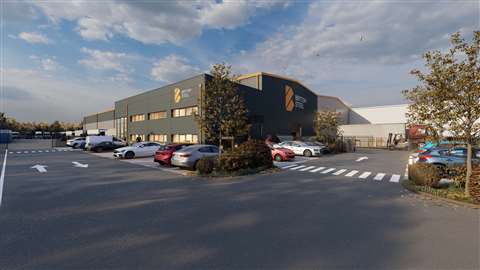
British Steel is to invest £26 million in a new special profiles processing centre at its Skinningrove site in Middlesbrough.
Special profiles are used to manufacture construction equipment, such as earthmoving machinery for heavy-duty applications and forklifts.
Described as “almost recession-proof”, the material handling equipment sector has seen the demand for forklifts continue to rise.
While much of this is attributed to the growing popularity of online purchasing and delivery services across all sectors, new infrastructure spending introduced by the Government by counter the economic impact of the pandemic - as well as large-scale projects like HS2 - are also thought to be key factors driving the demand for forklifts and earthmoving equipment.
The new 8,000m2 downstream processing facilities at British Steel’s Skinningrove site will comprise new cut-to-length lines, product milling, machining and warehousing operations for the manufacture of special profiles.
According to British Steel, which was bought by Chinese conglomerate Jingye Group in March 2020, the investment is the largest the company has made at the site for more than 30 years and is part of a £100 million project that aims to improve its “manufacturing and environmental performance”.
In an exclusive interview with Plantworx News, David Waine, British Steel’s Commercial Director of Special Profiles, said, “Jingye bought us with a plan and they are starting to do what they promised. They promised that they would spend £100 million this year, and we’re starting to realise that through the different investments that are going on.”
He added, “We’re looking at our plans in terms of sustainability for the future and our decarbonisation road map…We’ve got to adopt new industry expectations so we’re looking at how we can develop for the future and what we’re going to do.”
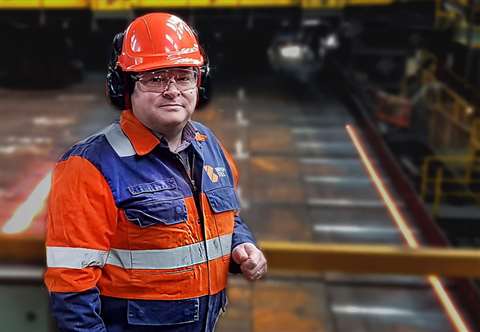
Reducing carbon emissions in the steel industry
Work on the new steel processing facilities is expected to start later this year, with completion set for August of 2023.
While it will mean closure of British Steel’s Darlington site, which stores and cuts profiles to customer requirements, the investment will almost quadruple the volume of special profile products further processed by the company and see it cut CO2 emissions from its logistical operations. The 25 Darlington employees will be offered other roles within the business.
Waine said, “If you look at what we do at Darlington, we’re limited by the size of the operation there as to how much volume we can put through.
“Darlington has been limited to 15,000 tonnes a year, and ideally we want to grow to 55 to 60,000 tonnes a year of particular products through this new centre.
“One of the biggest benefits, more than anything else, is that Darlington is 35 miles away from Skinningrove. As well as sending products for processing at Darlington, we also have a roll turning and engineering workshop on the site.
“At the moment, we transport rolling equipment between Skinningrove and Darlington for overhaul - our new facility will mean these journeys between the two sites will no longer be required as we’ll have the capability to do this work at Skinningrove.”
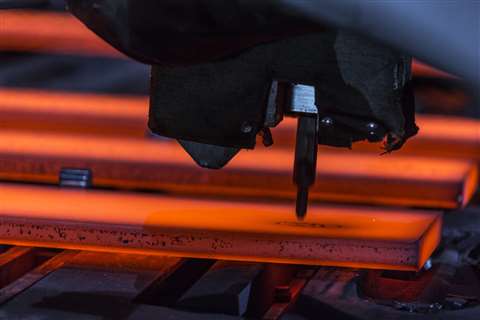
Steel market growth
Waine added, “Whilst we identify that most of the growth is going to come from what we believe is the forklift truck industry, the kit that we’re investing in will help us across all sectors,” said Waine.
“It’s really, really positive. The new processing capabilities it will give us is going to be quite huge.
“Some of the additional machines that we’re getting means that we’ll be able to do so much more than we’re currently capable of offering, and we know that our customers are needing those types of processing capabilities.”
He added that while British Steel is looking to streamline its operations, its increase in steel production will mean that the company will “probably actually end up needing a couple of extra people”.
While the entire construction industry is experiencing an alarming skill shortage, British Steel has managed to keep the impact of this at a nominal level.
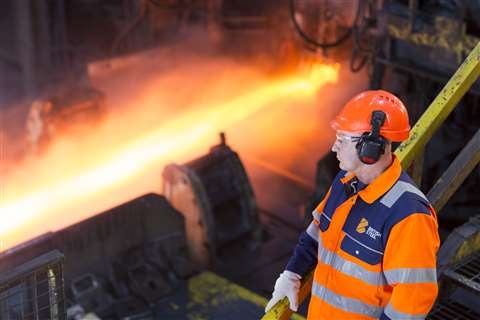
Steel industry skills shortage
Waine said, “It’s a strange kind of thing, the steel industry, because we have seen the UK steel industry decline quite significantly over the years – in terms of volume and the number of people employed as new technology comes in.
“But certainly, in our area, up in the north-east with the Teesside beam mill and Skinningrove, you’ve got generations of people that have worked in the steel industry.
“One of the things British Steel has been really, really good at is maintaining the number of apprentices that we bring on,” says Waine.
“Every year we bring on a steady stream of 20 to 30 apprentices to try and train them up into the jobs and fill the skills in the trades that we need the people in to keep the mills running because, one thing’s for sure – these are specialist types of roles.
“What you learn in the steel industry, you wouldn’t be able to walk out of the steel industry and get exactly the same job in many cases. So we’re always keen to bring on the next generation.”
He added, “The Government’s apprenticeship programme has been one that we’ve heavily supported and then every year we’ll take a selection of graduates in across different functional roles.”
Construction industry supply chain
In addition to a nationwide skill shortage, the UK construction industry - like others around the world - is also facing supply chain issues.
While British Steel has not suffered any problems with obtaining the materials it needs to make steel, it is not immune to the logistical problems being faced by the country as a whole.
Waine said, “We’ve not really faced troubles with our raw materials and in essence we’re making more this year than we did last year, so we’re producing more and focusing on timely delivery to our customers.”
“And then obviously as well there has a been a surge in prices, for container shipments for example, so generally all logistics costs have increased quite significantly.”

UK steel industry post-pandemic
When asked about the challenges brought on by the Covid pandemic, Waine said that while it had been “a very, very busy year”, the outlook was positive.
He said, “You know, the steel industry is always cyclical, but at the moment, global demand seems to be riding high.
“We’ve all bounced back from a lot of the Covid shutdowns and furloughs and everything that we and our customer base faced last year. It’s really positive to see the world economy generally bouncing back.”
Got a story?If you have a UK construction industry news story or project that you would like us to write about, email news@khl.com |