Case study: UK city’s Tower of Light
06 January 2023
In 2021, Arup and architects Tonkin Liu unveiled their Combined Heat and Power Plant Tower of Light structure in the heart of Manchester in the UK.
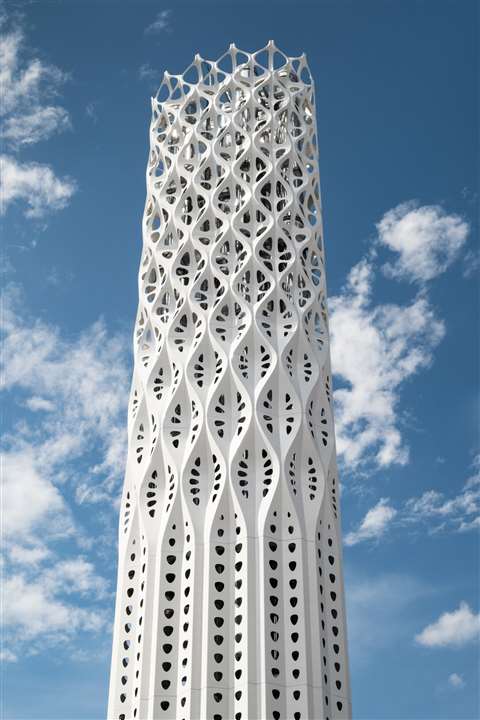
This nine-storey, 40m-tall tower structure supports and encloses chimneys for the city’s low carbon energy centre. It serves heating to a number of iconic buildings, including The Bridgewater Hall and Manchester Town Hall, with its energy used across a district spanning 2km.
The team won the project in Autumn 2017, based on a collective vision inspired by the natural world which ensured the strength required for the building’s vital purpose would not jeopardise its material usage, efficiency, or aesthetics.
This meant an integrated approach formed of energy efficient engineering and design excellence.
Energy efficient engineering
Contributing to Manchester city’s target to reach carbon neutrality by 2038, the building incorporates energy efficiency in all aspects of its engineering and design.
For example, heat from the power-generating engine is used to create hot water, which is then distributed through insulated districted pipework across the city.
This technology saves Manchester 1,600 tonnes of carbon emissions annually and improves the Tower of Light’s efficiency by as much as 45%.
Clever engineering also means the lights on the tower, which create a backdrop of light sequences and animations, are powered by the wind.
The wind causes reflectors in the tower to move and reflect sunlight into the tower’s chambers during the day, and in the evening LED lights are directed at the reflectors to have the same effect.
This enables the structure to act as a source of entertainment for passers-by, without impacting its efficiency.
The Energy Centre, which stands next to the tower, is also efficient in that it has been built with the ability to adapt to future change in demand; it currently contains a 3.3MWe combined heat & power engine and two 12MW gas boilers but has the capability to add future energy technologies without disruption to the supply.
Design with purpose
The Tower of Light’s architecture and design was considered just as important by the team as its energy efficiency, leading to a unique façade grounded in the latest advanced digital modelling, analysis and fabrication techniques.
This technique is known as a Shell Lace Structure, and has been pioneered by Arup and Tonkin Liu together for over a decade.
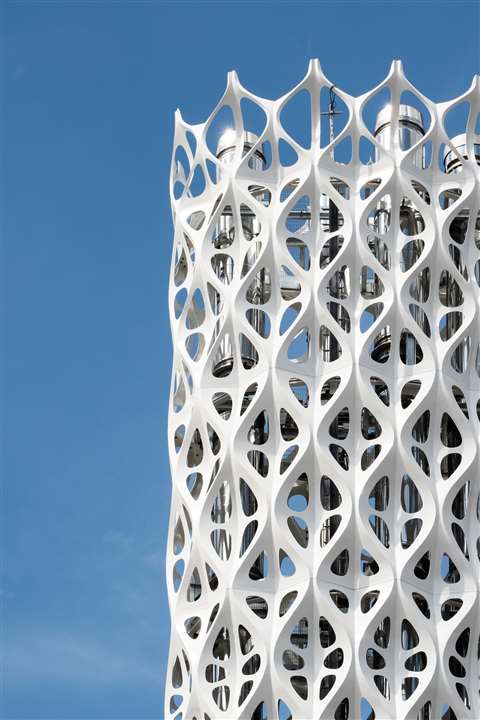
The Tower of Light is the largest built structure using this method to date. It uses a light and thin surface, which functions for design purposes while also using as little material as possible to boost the structure’s sustainability credentials.
The flat steel sheets which make up the tower are between 6mm and 8mm thick at the bottom of the tower, and at the top of the tower just 4mm.
The strength is provided by cut plates which are bent and welded together at the seams, meaning no additional structural support is required.
Similarly, the Wall of Energy, a 63m-long and 4m-to-6m-high street façade structure which encloses the new energy centre, is an example of design built with nature in mind. It is made of a tessellated interlocking lozenge tile pattern, composed of 1,373 tiles using 31 different tile types.
These reflect and mirror both the busy city centre streets and the sky, demonstrating the building’s links between the natural world and the built environment.
Chris Clarke, Tower of Light project engineer with Arup, said, “The Tower of Light shows what is possible when engineering and architectural principals merge, in conjunction with the use of digital design and fabrication techniques – we can integrate highly efficient use of materials with visual elegance to create something useful.”