Improving and optimising construction progress monitoring
06 January 2023
Bahadir V. Barbarosoglu, Ph.D., Program Manager, Linesight
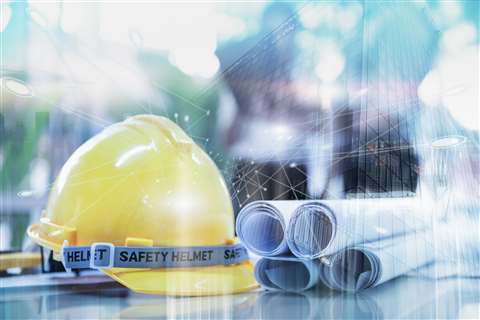
Construction site-walks have long been recognised as an important mechanism for keeping projects on time and budget. Up until recently, however, there’s been little innovation in this area. In the 21st century, clipboards and paper documentation finally gave way to mobile devices and digital progress management software. But the process continues to mostly rely on data collected manually by the various industry practitioners on the construction site.
That opens the process up to the error inherent to any subjective, manual process. Additionally, contractors, whose payments often depend in large part on the results of such walk-throughs, have misaligned interests with the project manager, which makes the prospect of good faith interpretations even less likely. In short, an unsystematic approach to construction monitoring can actually be worse than not monitoring at all.
All that helps explain why construction progress monitoring has started to attract attention from construction technologists, as it represents an opportunity for builders to gain a competitive advantage. Their research has aligned around the buzzword ‘automated construction progress monitoring,’ which refers to technologies that eliminate manual processes and human errors by automating construction progress monitoring and status updates.
Extension of BIM
These technologies can be understood as a continuation of building information modeling (BIM). With BIM, projects are simulated in a 4D virtual environment that integrates a 3D model with the project schedule. BIM incorporates real-time data, including progress data obtained from site walk-throughs, to provide enhanced reporting to project managers. But BIM alone can’t do anything about the quality of the progress data coming in and on which its models are based. That’s where automated construction progress monitoring can make a difference.
In practice, you’ll see three major technologies used to enable automated construction progress monitoring: laser scanning, photogrammetry and videogrammetry.
Photogrammetry refers to the science of obtaining measurements from photos. In photogrammetry, three-dimensional coordinates are calculated using multiple pictures of an element taken from different positions.
Videogrammetry is actually a branch of photogrammetry. Videogrammery obtains three-dimensional coordinates of an object by using images extracted from video frames. It has the edge over photogrammetry when it comes to capturing dynamic elements. Generating point clouds using the laser scanning method is usually more expensive than its alternatives, and it requires skilled operators and a relatively longer duration to process the point cloud data.
There are other potential downsides, including long data processing times and lower quality images resulting of electronic noises. Considering time, quality and cost constraints, photogrammetry is often the most feasible method of generating as-built point cloud data. That said, the construction progress data acquisition method should be always selected based on the specific nature and dynamics of the project at hand.
Photogrammetry can involve either fixed or moving cameras. In a fixed approach, cameras set up on the construction site are programmed to capture images of construction progress of a particular space or element of the project at predetermined intervals. The images are then evaluated to determine whether the detected changes are following the plan indicated by the 4D BIM model. When combining image sets from two cameras covering the same area 99% accuracy can be achieved.
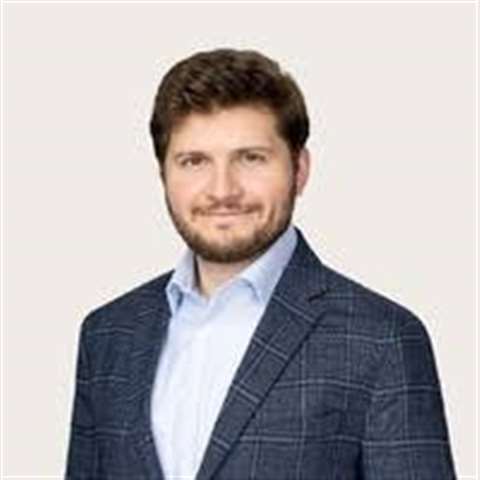
Moving camera photogrammetry uses image processing and deep learning algorithms to process images taken from mobile cameras, such as mobile phones, and tag key objects in their frames. The automated construction progress management system then compares the images of these objects over time to determine their progress status. A 2020 case study found that the accuracy of these image processing technologies in detecting construction progress is dependent on data labeling quality.
UAVs and construction
The major area of excitement in the automated construction progress management space is research into drone - or UAV (unmanned aerial vehicle) - mounted systems. UAVs can be programmed to follow predetermined paths, capturing images along the way. Progress pictures captured by UAVs can then be processed using image processing and optimisation algorithms and integrated with 4D BIM platforms.
A UAV-mounted system was recently tested through case studies, which validated that the system can successfully conduct automated progress monitoring for specific targets. Such a system would likely be faster and less expensive than automated construction progress management performed by unmanned vehicles or robots.
Regardless of the specific approach, BIM integration is non-negotiable. With the findings of recent case studies and the wealth of industry applications, automated progress monitoring systems could soon be a common sight on construction project sites.
Bottlenecks towards efficient and economical use of automated construction progress monitoring systems, such as nonstandard data collection and processing procedures, remain. These areas are where academia and the construction industry should focus their attention and continue working collaboratively to establish best practices and standards for automated construction monitoring systems.
Dr. Bahadir Barbarosoglu is a program manager at Linesight. He is an enthusiast of science, innovation, and engineering, and a Certified Professional in project management, risk management, planning & scheduling, agile management, earned value management, and cost management.