The need for net zero in construction
17 March 2022
The climate emergency means the construction industry must evaluate its carbon footprint and develop processes that meet wider sustainability targets and European initiatives - and quickly. Cat Jones reports.
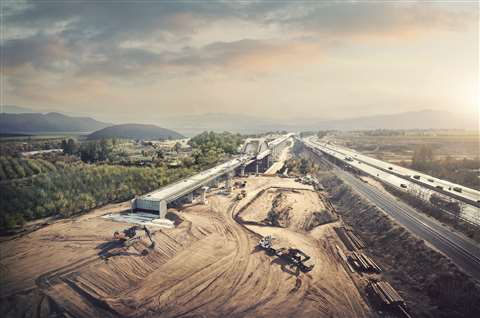
The recent COP26 summit – held in Glasgow, Scotland – demonstrated that sustainable infrastructure was necessary to reduce the 39% of energy and process-related carbon dioxide (CO2) emissions for which the construction sector is responsible. To achieve a net-zero future, the sector has a responsibility to reduce its carbon footprint and improve the sustainability of the built environment.
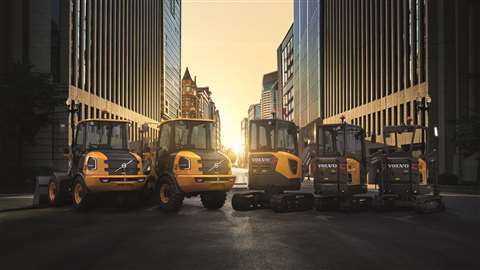
To help companies act, the Science-Based Targets Initiative (SBTi) – a necessary measure to meet the goals of the Paris Agreement – drives the private sector to take critical climate action by setting science-based targets to reduce emissions.
Volvo Construction Equipment (Volvo CE) says it is heavily committed to this initiative, and it is in line with the company’s long-term ambition to achieve net-zero value chain emissions by 2040, with significant emission reductions anticipated as early as 2030.
Committed to change
The target of net-zero value-chain greenhouse gas emissions by 2040 is a united commitment for Volvo Group across all the business areas and is set for 10 years earlier than the SBTi commitment, says Marcus Karlsson from Volvo CE Sustainable Power Systems. This is due to Volvo products having an average life of 10 years in the customer use phase. For the entire rolling fleet to have net-zero emissions by 2050, it is necessary that all products delivered after 2040 have net-zero emissions.
In the meantime, Volvo CE has also set its own interim goals to be met by 2030. These include cutting emissions in half in its operations, facilities, and manufacturing processes, and achieving 30% in absolute reductions in the use of its products.
Carolina Diez Ferrer, head of advanced engineering programmes at Volvo CE, explains how the company is also focusing on the impact it can make in its warehouses and facilities. “We are investing in solar-panelled cells in [our] warehouses and are looking at the other options available to us,” she says.
“One of our focuses is also on building a circular economy – raw materials will be kept longer in their cycles, and this will further fulfil our sustainability
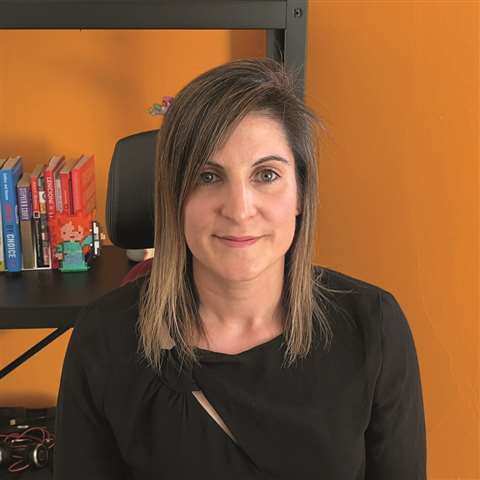
commitments.”
Hydrogen power
In a bid to meet sustainability targets, companies are redefining diesel-fuelled machinery and reassessing the impact these have on the environment.
Marcus Karlsson says, “Volvo has introduced compact electric machines and we are developing light to medium segment machinery that is electrified with battery.”
While battery-electric solutions are ideal for urban construction and other use cases, the size of the batteries is generally too impractical for larger machines and heavy construction equipment, says Karlsson, which is where Volvo CE believes hydrogen comes in as a promising alternative.
Volvo CE sees hydrogen fuel cell technology playing a key role within its overall electromobility ambitions, together with battery-electric solutions, as demonstrated by the electric compact machines, and more sustainable internal combustion engine offerings – with all three streams working in alignment on the journey towards a carbon-neutral society.
Decarbonisation of the UK
Balfour Beatty has recently announced that the Technip Energies and General Electric Gas Power consortium, in which the company is the construction partner, has been selected by BP to participate in a Front-End Engineering Design (FEED) competition for the Net Zero Teesside Power, Capture and Compression project.
The FEED competition will see Balfour Beatty assist in the design and development of optimal technical solutions for Net Zero Teesside Power’s planned 860MW power station and carbon capture plant, as well as the Northern Endurance Partnership’s high-pressure carbon dioxide compression and export facilities.
Stephen Tarr, chief executive officer of Balfour Beatty’s major projects and highways business, says the project “represents a significant milestone in the decarbonisation of the UK,” adding that, along with consortium partners, the company was “harnessing the spirit of collaboration” to tackle the climate change challenge.
Curbing carbon emissions
With the built environment accounting for 39% of carbon emissions globally, it begs companies to ask themselves – what are we doing to reduce this? Robert Spencer, environmental, social and governance (ESG) lead at Aecom, believes the ScopeX process is a valuable tool to help end the climate crisis by reducing carbon through clever design.
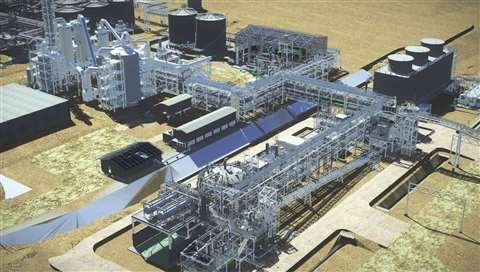
He says, “We launched our ScopeX solution with a goal of reducing embodied and operational carbon in the built environment that we can control or influence by 50%, particularly through design. We look at all areas of a project to minimise carbon emissions including materials, energy, and how we can work with natural habitats to enhance them and sequester carbon.
“This work has already started with some pilot demonstration projects and a basket of tools and dashboards to support the embedding of this carbon literate mindset across our engineering community.”
ScopeX aims to utilise customised technical approaches combined with a range of digital solutions to deliver significant tactical opportunities for lifecycle carbon reduction. Aecom is bringing together various internal and external processes to support this effort, including developing digital tools to quantify carbon impacts and provide optioneering and benchmarking, developing knowledge repositories to quickly upskill their technical staff, adapting internal processes to drive decarbonisation discussions into project delivery, and identifying collaborations with partners to address knowledge gaps that exist in the industry.
The manufacture of building materials and products, such as steel, cement and glass, combine to produce 11% of the construction industry’s carbon emissions. Aecom says more focus needs to be placed on implementing low carbon materials into projects to reduce this figure.
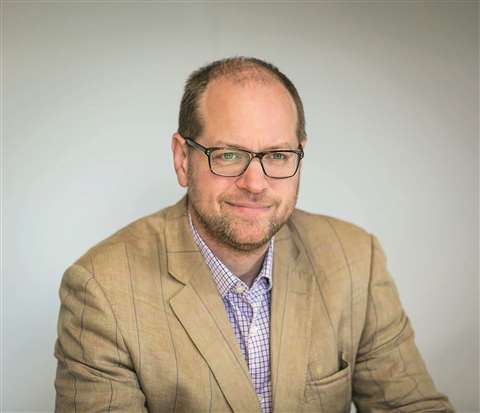
Spencer believes this is an area in which Aecom is excelling, saying, “We have a pavement engineering and construction materials laboratory at our UK Nottingham offices, which is dedicated to investigating the application of low carbon and recycled material content into real pavement environments for our road, rail and aviation clients. The team at our lab has been behind the pioneering use of warm mix tarmacadam and recycled content for airport pavements, for example.
“We also foster infrastructure client collaboration on this vital issue. We convened the Infrastructure Decarbonisation Forum (InDeFor), a client collaboration group for our major UK-based infrastructure clients. We recently held a dedicated session on low carbon materials with a particular focus on alternatives to concrete, steel, and asphalt in infrastructure.
“When considering low carbon materials, we believe priority should be given to the management of assets and infrastructure in a way that extends their service lives and reduces lifetime carbon.”
Will technology improve sustainability?
As technology advances, companies must develop and adapt accordingly while remaining conscious of environmental concerns and surrounding issues. Spencer is aware of the benefits of optimising projects through technology and embedding sustainability into what Aecom does to meet targets.
“We’ve recently launched Digital Aecom, bringing together our flagship digital innovations, tools, systems and processes which together transform programme management and delivery. We do this through supporting clients in their digital strategy, design and operations, embedding and optimising digital solutions and use of data analytics and AI.”
Why should Digital Twins be used in construction?
Digital twins and digital twin methodologies can apply to all phases of a structure’s lifecycle. The earlier that a project starts with digital twins in mind, the richer the data and insights, says Brian Robins, Bentley Systems’ VP of product and industry marketing.
“In terms of construction, we can aggregate the source data into a construction digital twin, which includes the design data and the construction information added during preconstruction planning. With the use of mobile devices for data capture, we can receive feeds from the construction operation including sensors, drone capture and overall site progress.”
Digital Twins can have a significant advantage in the early stages to ensure the build is mindful of its surroundings. Rich Humphrey, Bentley’s vice president of construction, adds, “Digital twins can help minimise the destruction on the environment by giving you the ability to virtually plan the build and determine how the infrastructure will affect the surrounding area.”
Additionally, linear design models of a project can be easily broken down into design components or parts and then be used to create a construction schedule based on, for example, how many people are needed and when they are needed.
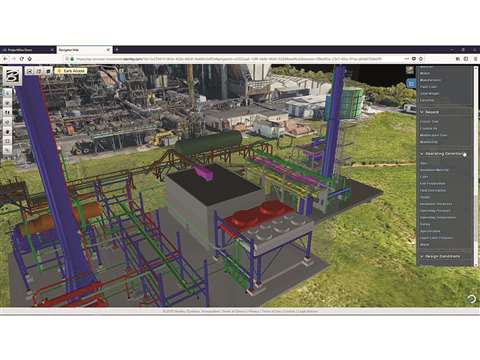
Robins adds, “We can use digital twins for QTO [quantity takeoff] to estimate what manpower and material you will need to get your project off the ground. This labour and material cost determination, which is usually done manually, can now be automated to calculate cost estimates for material quickly and easily.
“Digital twins help users make data-driven decisions and achieve predictable results. All construction-related information is available in one place, including asset tags, work orders, maintenance records, inspection records, and work schedule details. Everyone involved in the project can exchange project data and information between the construction site and the office and access it at both locations. The project team has all the tools and information needed to perform analysis and use the intelligent data to make informed decisions.”
In the case of iTwins, Bentley believes its digital twin technology will extend over the entire lifecycle of the project, from planning to execution and operation, so that users can improve collaboration and make more informed decisions and achieve better results in all phases.
According to Robins, iTwins allow users to simulate logistics and project schedules, track progress, complete status reviews and view an up to date 4D model.
He says, “All the sources of data discussed – some static but many near real-time – make up a rich project digital twin valuable for linear projects and horizontal construction projects. A digital twin allows for project visualisation which enables users to quickly run construction sequences and simulations so that they can identify and correct errors before construction starts.
“Project teams reduce the overall time on site by conducting the project analyses before going to the construction site and, thus, reducing the costs for the client.”
Bentley’s Synchro 4D modelling technology enables the end-user to plan, schedule and control the on-site aspect of a project, both virtually and visually. Robins believes that all these functions result in a step function improvement in productivity.
Q&A with Ramboll
Is Ramboll changing the way they build (using new technology to make projects more efficient)?
The North Zealand Hospital - an example of design that focuses on social, economic and environmental sustainability (Photo: Ramboll)
Yes, we are designing modular or pre-fabricated buildings whenever feasible to decrease overall costs and improve quality.
Is Ramboll looking at low carbon materials?
Going forwards, we will be specifying the materials with the lowest carbon footprint are used in our designs. For many materials (like concrete, steel, aluminium and insulation) there are lower carbon options available at no additional cost, but if you do want materials with a dramatic carbon reduction you could end up paying a premium. Ultimately, our clients are having to strike a balance between costs and carbon.
Has the European Green Deal changed anything for Ramboll on a day-to-day basis?
The European Green Deal is leading to a lot of new regulation that will dramatically change the construction sector. New regulation, such as EU Taxonomy reporting, the Energy Performance of Buildings Directive, and Circular Construction initiatives will have a significant impact on the sector, particularly for suppliers of materials and components – those who cannot offer a low carbon option in the future will soon find they have no market.