What are the latest below-the-hook products?
27 September 2022
Each year, American Cranes & Transport checks in with makers of below-the-hook rigging gear to determine what’s new in this ever-evolving sector of the lifting industry.
Below-the-hook rigging encompasses a wide variety of products, and moreover, it’s become an area in which automation is increasingly being applied.
The goal is safer, more productive lifting projects. Following is our annual roundup of products, news and information relevant to below-the-hook rigging.
Ashley Sling’s largest roundsling yet
March 2022 marked the 30th year of business for Ashley Sling. The family-owned company made it their mission to provide quality lifting products and services to their customers, according to the company.
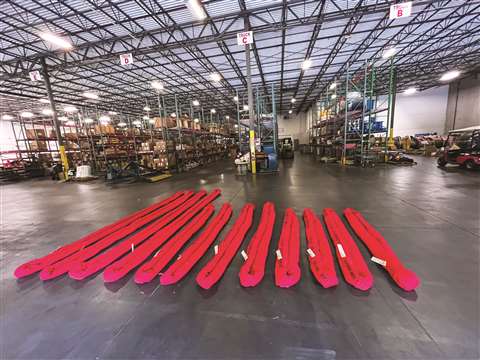
“The small business quickly became a leader in the wire rope and rigging industry in the Atlanta, Georgia area and extended their reach across multiple locations in the southeast,” said Julianne Jordan, marketing director. Today, there are four different branches located in Atlanta, GA, Charlotte, N.C., Columbus, MS and Knoxville, TN.
“While the industry evolved, Ashley Sling remained constant in its mission to provide high quality lifting products,” Jordan said. “The HPZ Extreme Lift Roundsling is one example of the company’s drive to continue offering products that best serve customers.”
The HPZ Extreme Lift Roundsling is a high-performance sling made from a custom blend of HMPE and Aramid fibers. The fibers are enclosed with Ashley Sling’s TUFF-ASH two-ply red outer/yellow inner jacket.
“The HPZ Roundsling offers a superior strength-to-weight ratio, which allows for easier handling,” she said.
While Ashley Sling has fabricated the HPZ Extreme Lift for several years, the company recently released its largest size yet, the HPZ 250. The HPZ 250 has a vertical rating of 250,000 pounds. A wire rope sling with similar strength weighs 30 pounds per foot, while the HPZ 250 is only 5.25 pounds per foot. The HPZ Extreme Lift Roundsling allows for heavy lifting, while also providing an ease-of-use that wire rope slings simply cannot, Jordan said.
Innovation will continue to be an integral part of growth for Ashley Sling and the industry as a whole, according to Greg Ashley, owner and president.
“We are thankful for our achievements over the last 30 years, and we look forward to what lies ahead for Ashley Sling,” Ashley said.
Remote-controlled hooks from OTH Pioneer Rigging
Montreal, Quebec-based OTH Pioneer Rigging has launched a new line of lifting hooks that are remotely controlled to allow workers to release rigging from loads safely from a distance. With unlimited hooks synchronized on the same remote, users can design their own setup.
Both models, with a 4,400-pound and 11,600-pound working load limit, work with vertical, basket or choker setups and any kind of attachment (wire rope, nylon rope, chains, eye bolts, etc.) to lift up to 100,000 pounds.
For high cycle tasks such as steel erection, wood framing, components delivery or trans-loading, the remote-controlled hook can save up to four hours of the time it takes to release loads over the course of the day, the company said.
The remote control is color-coded to coordinate with hooks, which can be opened all at once or one at a time. With a range of 200 feet, the remote control triggers an opening mechanism, and a two-button release sequence is required to open the hook. This below-the-hook lifting device features a mechanical fall protection design that switches off the opening mechanism of the hook during the lift.
“The rugged design and streamlined shape of the hook is designed for work in harsh environments and features long-lasting battery life, capable of making more than 100 lifts per day for a full week before recharging is required,” OTH said. “The hook remains locked if the battery is fully discharged.”
With more than 400 units already in use in North America, these hooks are ASME, UL/CSA and FCC/IC compliant. OTH Pioneer Rigging offers new users the opportunity of a one-week free trial.
An error in semantics
Lifting beams and spreader beams are significantly different in both appearance and by functional definition. Industry “slang” terminology, however, creates a semantics error, often mistaking which lifter is required on the job by calling both a “spreader beam.” There is a distinct difference between the two and can be explained by examining both beam styles.
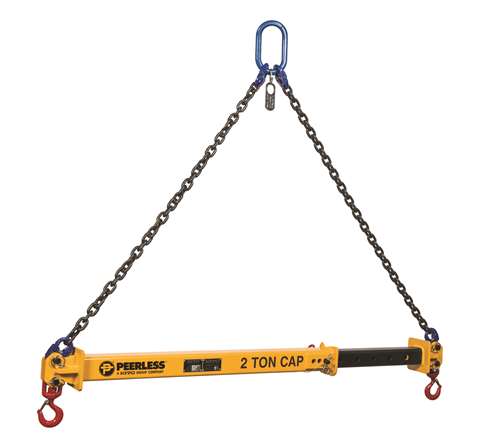
Lifting beams attach directly to the crane or hoist hook and deflection occurs outward from the center. The strength when lifting is derived from the beam material and configuration. Lifting beams can be manufactured from round or square tube, channel or I-beams.
As the device increases in capacity, the use of I-beams becomes the dominant steel required to attain the higher working load limits. Lifting beams are often supplied with multiple pick points that provide adjustability based on the load configuration and center of gravity (CG). Lifting beam design allows for the opportunity to have a low center connection to the hoist hook for areas where headroom is a major concern. They can be engineered as low headroom devices that are often required for critical lifts.
Each lifter can be portrayed in a variety of configurations. Lifting beams can be as simple as a triangular short span lifting beam with two lifting points that are one foot apart to a complicated 4-point adjustable lifting beam with multiple pick points. They can also be used with a single cane or synchronous dual cranes if required.
Spreader beams require top rigging to support the load. The effect of lifting the load with a triangular configuration forces the beam to lift with compression on the beam rather than the deflection that occurs with a lifting beam. This creates a slight advantage to using the spreader beam over a lifting beam in that it provides much more stability.
When using a lifting beam, the load CG must be centered exactly under the crane hook to attain a level lift. The spreader beam does not require that the CG be as exact. The extra top rigging also exemplifies the fact that a greater amount of headroom is needed to lift and transport the load.
More limited configurations
A spreader beam has limited configurations available to the rigger. Spreader beams can be fixed or adjustable. They can also be comprised of square or round tubing in a box-style spreader beam design. End Cap Spreader Beams allow the rigger the opportunity to stock a variety of different lengths to accommodate different loads. They must follow a matrix that will change the lifting capacity based upon the length of pipe being installed.
When ordering either style of lifter, it’s important to request the correct device that is required. Each one has limitations that make it the preferred choice to make a required lift. Finally, verify that the beam is designed in accordance with the ASME B30.20-BTH-1 design criteria with the applicable design category and service class. The beam is also required to be proof tested to 125 percent of its rated capacity before placing it into service.
Peerless offers both lifting beams and spreader beams from its range of products. Peerless has been providing best-in-class products, innovation and custom solutions to a diverse industrial and consumer customer base for over 100 years.
― Bob Kozickie, Technical Sales Support Manager, Peerless
Green Pin solution
The lifting industry is always looking for solutions to prevent the dropping of equipment and components from heights. Dropped objects are a well-known safety hazard and are a leading cause of accidents.
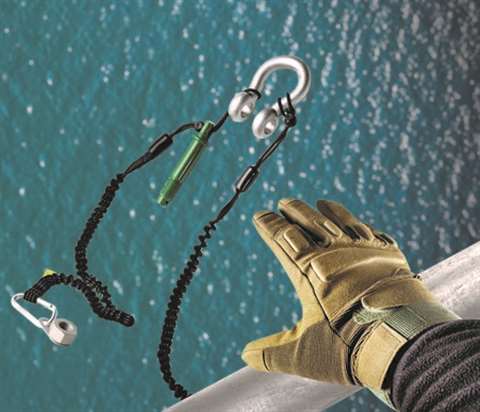
Green Pin offers a unique solution to this problem. The Green Pin Catch shackle prevents the accidental dropping of shackle bolts, nuts, cotter pins and even complete shackles.
These innovative shackles have an attachment point on each individual component to connect them to a lanyard. The lanyards can then be securely fastened to something or someone, for example, to a tool belt that the rigger is wearing.
The disc on the nut that enables tethering rotates independently from the nut itself, thereby not coiling the attached lanyard. The Green Pin Catch Shackle is supplied without any wiring so every user can choose their preferred method of securing the products.
In addition to the tethering options, the shackle offers a double safety (split pin and safety bolt) which prevents accidental unscrewing of the pin. The Green Pin Catch Shackle conforms to a wide range of certifications and industry standards, the company said.
Jergens’ Lift-Check hoist ring
Jergens’ new Lift-Check hoist ring ensures safety and quick lifting with its patented, proprietary Visual Tension Indicator hex-head cap screw. These screws turn from red to lift-check “jergens black” when the hoist ring is safe to lift – eliminating calibration, allowing hands-free inspection and significantly reducing installation time.
Essentially, red means no and black means go. Lift-Check provides accuracy of plus 10 percent of designed tension and are rated at 5:1 strength factor and proof tested to 200 percent of rated load capacity in accordance with ASME B30.26. Made of alloy steel with a black oxide finish, the Lift Check Hoist Ring offers full 360 degree swivel and 180 degree pivot action.
Built in the United States, Lift-Check provides repeatable solutions for a wide range of lifting applications from 2,500 to 7,000 pounds. Lift Check’s U-bar, bolt, pins, base, washer and bushing are magnetic particle inspected. Jergens also offers Lift-Check bolt kits for standard and long U-bar styles.
New super reever from Associated Wire Rope & Rigging
“Our new Super Reeve Connector Swivel Socket (SCS-SW) is a revolutionary evolution of the Fast Connector Socket,” said Curt Jabben, director of North American sales and marketing for Associated Wire Rope & Rigging. “This socket line has the smallest connector diameter available in the market today, and still meets the respective EN standards. It has been designed to go through the smallest spaces in a crane reeving system. This unique patented design allows refitting by pouring the button in the field, saving valuable down time compared to swaging techniques.”
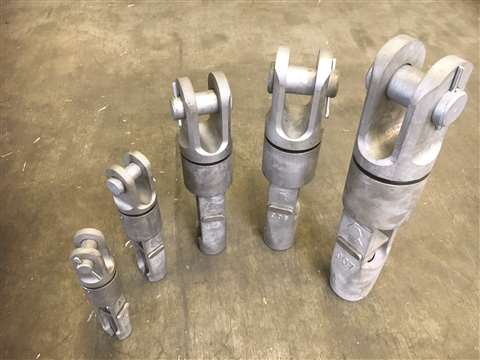
The reason why a swivel is used so often in the dead end is that it reduces the torsional forces acting on this area, which are caused by factors such as the fleet angle at the sheaves. These torsional forces can cause significant damage to the cable, leading to crane downtime or even unsafe situations. A loose socket and a loose swivel are often used for cranes.
Wedge sockets achieve an efficiency of 80 to 90 percent. The Super Reeve Connector Swivel socket tops that by achieving an efficiency of 100 percent, Jabben said.
“We also reduced the overall length by integrating the swivel in the socket,” he said. “Our new Super Reeve Connector Swivel Socket offers a host of practical benefits for many crane types. The shorter overall length optimizes the hoisting height, meaning that it is ideal for hoisting inside buildings and in other situations where hoisting height is critical. In addition, integrating a swivel increases safety as the torsional forces referred to previously are reduced significantly in comparison to situations where only a socket is used.”
Associated Wire Rope & Rigging based its solution on patented and proven technology, Jabben said. This socket is a more cost-effective solution than the conventional combination of separate swivels and sockets. They are designed as a universal product that can be relatively easily adapted to all types of cranes. This makes these swivel sockets suitable for both end-users and OEMs, in many industries and applications, he said.
Generator overhaul
Modesta, CA-based TCB Industrial recently undertook a powerhouse plant maintenance project to overhaul a hydroelectric turbine generator. As part of this project, they needed to lift and articulate the turbine’s rotor into a vertical position.
“We were essentially doing something that’s never been done,” said Scott Gomez, TCB Industrial project manager. “This is the first time this horizontal unit has been placed into a vertical position.”
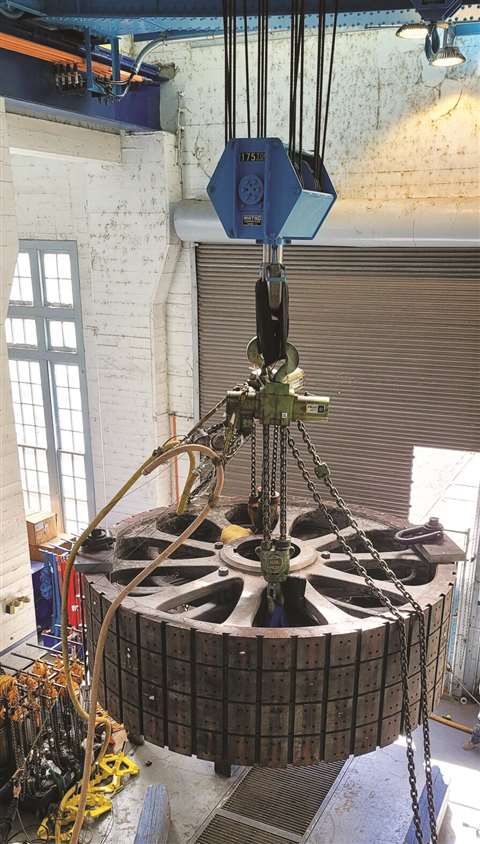
Faced with an unconventional way of doing things, TCB Industrial knew they would need a unique rigging plan for this project.
“Since this hasn’t been done before, our team designed and engineered the entire rigging plan, including all the rigging brackets we used,” Gomez said.
The TCB Industrial team had to consider several factors when designing the rigging plan. Accessibility, headroom restrictions and ensuring the rigging equipment had a high enough capacity to support the rotor were the primary considerations.
The TCB team settled on a rigging plan involving two 50-ton and one 60-ton capacity air chain hoists with two-inch bull pneumatic hoses.
“We didn’t want manual hoists because it requires more time and personnel,’ Gomez said. “The pneumatic hoists did all the pulling and allowed us to situate the load in the correct position using fewer people, thus reducing risk and cutting cost.”
Gomez approached LGH rental representative Beth Kolar with the rigging plan he devised, and she helped him get set up with everything on his list, as well as an accumulator tank that provides a reservoir of compressed air.
“Beth let me know that a single compressor wouldn’t be able to handle the draw required to operate two air chain hoists simultaneously without the help from an accumulator, so we ended up renting a 400-gallon receiver tank as well,” Gomez said.
Once all the equipment was assembled, the team got to work using the LGH pneumatic chain hoists, bull hose, receiver tank, an overhead gantry crane and a couple of man lifts. They assembled the turbine, took the rotor to the vertical position and began the overhaul on time and according to plan.
“We could have easily kept the unit in the horizontal position, but the powerhouse doesn’t have a lot of room for work,” Gomez said. “Putting the rotor in a vertical position only took up a 12-foot diameter versus 40-foot in the warehouse. So, it saved a lot of space being able to do it this way.”
Mazzella’s full-service spooling truck
Mazzella Companies has expanded its footprint in the lifting and rigging industry by building a new full-service specialty rope spooling truck and trailer in the Great Lakes region, based out of Cleveland, OH.
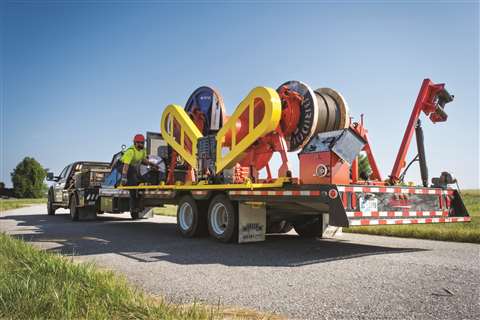
The design of the truck, and training of the technicians, makes the installation process easier for the end-user, according to Mazzella’s Matt Florjancic.
“Mazzella loads a reel of pre-cut rope at one of their facilities onto the truck and drives the rope out to wherever the customer may need it,” Florjancic said. “The uniquely designed spooling truck and trailer has two A-frames on it, which allows for a new reel and an empty reel, all on the same vehicle.”
From start to finish, it’s a time and cost-saving experience for the end-user, he said. Additionally, Mazzella’s installation process offers a value service by taking back the old wire rope and properly disposing of it. Mazzella stocks a variety of high-performance ropes at many locations in sizes from ¼ to 3-inches diameter and 9 to 52 millimeter diameter – with both domestic and non-domestic products in stock.
Elebia automating hooks
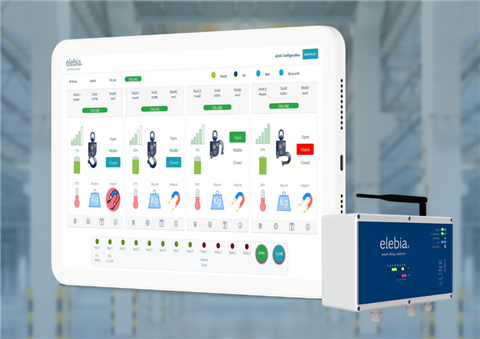
Elebia has launched eLINK, a smart tool for automation and safer lifts. The eLINK is a central data acquisition and control system. Its main operating function is to control Elebia lifting hooks through a web application that can be accessed with any smartphone, tablet or computer. eLINK’s in/out capabilities allow crane automation using the hook’s sensors data all in a quick, flexible and simple way.
User defined logical rules can be used to automate crane behavior, increasing jobsite productivity, enhancing safety, offering remote support and providing load tracking data. It is highly customizable. The eLINK’s “Over the Air” update capability allows for the addition of new features.
Protecting slings by DICA
DICA’s LiftGuard Magnetic Sling Protectors prevent damage to slings caused by contact with edges, corners or protrusions. They are available in multiple sizes and configurations, and can be used with synthetic, wire rope or chain slings.
“Sling protection is either good or its bad,” said Mike Gelskey Jr., president and general manager of Lift-It Manufacturing. “Many users rely on materials they have on hand, such as cardboard, tire rubber, retired slings and even hand gloves. These products do not have a protection rating nor the engineer pedigree to support their use as a sling protection device. Good sling protectors are engineered, with clearly defined usage guidelines and care and maintenance information.”
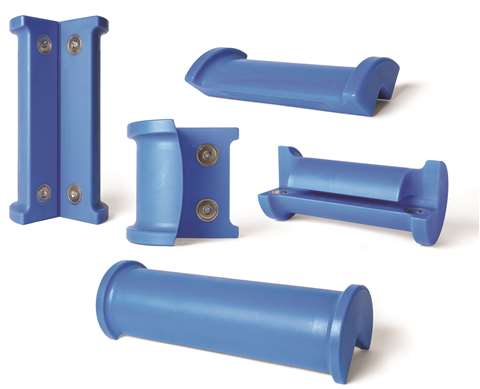
He said that increased demand for engineered sling protection has led to many new product introductions.
“In our opinion, one of the best is LiftGuard, which is one of the most durable and easy-to-use protectors on the market,” Gelskey said. “It’s frequently used when lifting steel plates, steel coils, I-Beams and wood crates.”
In terms of sling protection, users need to decide the best option for their application.
Many things must be considered, such as coefficient of friction, temperature, chemical resistance, etc.,” said Gelskey. “Only a qualified rigger performing the lift can determine which product is best suited for the specific application by reviewing product user manuals, protection ratings and warnings.
Bishop Lifting Products, a portfolio company of Altamont Capital Partners, has completed the acquisition of All-Lifts, based in Albany, NY. All-Lifts was founded in 1966 and has been owned and operated by the Dewey family since 1978. Since then, the company has grown into a leading fabricator of wire rope slings, synthetic slings, alloy chain slings and below-the-hook lifting devices. Brian Dewey will assume a leadership role at Bishop Lifting Products.
All-Lifts marks Bishop’s eighth acquisition since 2012 as part of Bishop’s ongoing strategy to build the company into the country’s leading provider of lifting products and services. Through scale and an expanding geographic footprint, Bishop will be able to deliver even greater service and lifting solutions to customers. Including All-Lifts, Bishop has 26 locations across the country offering a full line of lifting products and services. All-Lifts will continue to operate with its full workforce.
“We’re excited about our first acquisition with our new partner Altamont Capital and to continue our successful strategy of building Bishop through acquisitions and sound business strategies,” said Harold King, president of Bishop Lifting Products. “All-Lifts has a rich history as a family-owned and operated business and we are proud to welcome Brian Dewey into the Bishop Lifting family, working with him to continue his family’s legacy and leaning on him and his team to help fuel the growth of our combined platform. All-Lifts will be a great addition to our footprint in New York and the Northeast as we continue to build out our national footprint and continue our focus on high quality products and customer service.”
The Slingmax Equalizer Block
The Slingmax Equalizer Block (SEB) is a rigging device designed to be used with Slingmax Twin-Path high-performance synthetic fiber roundslings. The block maintains tension on all legs of a sling during a lift. When pressure is put on the device, the sling adjusts and equalizes the load on any pick point. This also makes the Equalizer Block an ideal tool for adjusting from horizontal to vertical planes, Slingmax said.

Available worldwide in 10, 25, 50, 75 U.S. ton and 125 metric ton capacities, the frame is constructed of steel with a synthetic polymer sheave specifically designed to grip the external cover of Twin-Path Roundslings. The bail is designed to work on both the bow and the pin of a shackle.
During a recent project, Frederik Stuart, P.E., senior project manager, considered steel equalizers and plates with wire rope rigging but preferred synthetic roundslings.
“We wanted to utilize synthetic rigging because it is so lightweight for its capacity, and it is a lot easier for the guys to work with,” Stuart said. “We couldn’t find anything that would work as an equalizer with synthetic slings before Slingmax offered the Equalizer Block. Without it, the options were limited on using synthetic slings. It really just opens the door to opportunities with the lightweight synthetics. Our guys in the field would much rather use a synthetic that they can throw over their shoulder as opposed to a heavy wire rope sling that you need a crane to move.”
Load stabilization with Vita Industrial
Vita Industrial recently partnered with Creative Lifting Services (CLS) – on a job in Boulder, CO – to deploy their flagship load stabilization system, the Vita Load Navigator. The Navigator, used on the assembly of a Jaso tower crane, enabled CLS to dispense with taglines and remove rigging personnel from the load path – making the jobsite safer.
“One of the biggest challenges we have when erecting a tower crane is running long taglines through a congested jobsite,” said Josiah Rausch, CLS crane tech manager. “Using the Vita Load Navigator meant we did not have to have riggers run through an obstacle course while holding taglines.”
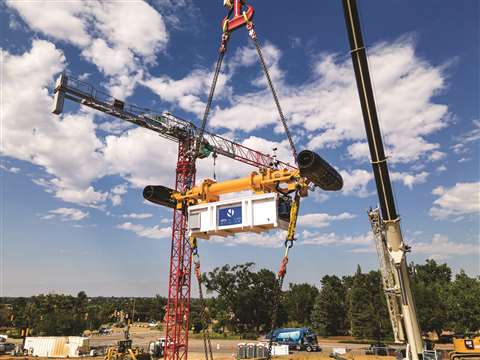
The Navigator was particularly helpful in the assembly of the tower crane’s horizontal jib, as it eliminated the possibility of the assembly piece spinning into the crane while being lifted, according to the company. Thanks to the Navigator’s dual pendant system, the crew member on the ground controlled the Navigator as it rose and then transferred control to the crane tech harnessed in at the top of the crane to guide the placement. By using two remote pendants, the CLS crew members were able to navigate the crane assembly pieces independently and efficiently, maintaining complete control and line of sight throughout the lift.
The Vita Load Navigator operates using four high-powered air thrusters to prevent unwanted load movement during crane lifts. Users can manually control the load within a single degree of deviation, or they can let the Navigator automatically stabilize and hold its position. This successful use of the Navigator to assemble a tower crane was one of many major milestones to come in demonstrating the benefits of load stabilization.
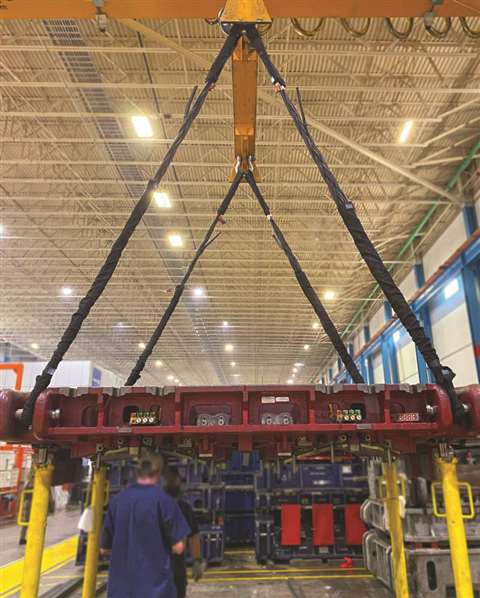
Yale Cordage Fortis2 Sling
When a Union, S.C. automotive stamping plant ran into issues with massive repair and replacement costs on their conventional high-capacity synthetic round slings, they turned to Yale Cordage to provide a winning solution. Yale’s Fortis2 Sling – a multi-part eye/eye sling made from Yale’s Unitrex synthetic cable – offered a rugged alternative to saggy round slings at a comparable weight and price point.
The constant need for sleeve inspection and repair was leading to lags in production time and extra cost for replacements. With Fortis2, the company found that the service life was five to six times longer than traditional round slings. This resulted in an extended service life per sling by 500 percent plus and returns upward of $50,000 per year for each sling.
Fortis2 Slings are built to be efficient, durable and more cost-effective than traditional round and wire slings, Yale Cordage said.
Yoke SupraTag
In the lifting industry, wire rope slings, chain slings and webbing slings are used to lift and move loads. This rigging gear must be constantly inspected for safety, which can be a timely and laborious process. The Yoke SupraTag enhances the security of any sling or lifting component, and the software “Ri Connect” enables workers to do a pre-use check of individual products.
Safe use instructions support learning to ensure sufficient knowledge and experience to fully enable users to know what to look for and how to address any issues.
SupraTag on slings with Ri Connect enables users to acquire such information as product traceability, declaration of conformity and manufacturer authentication.
This will assist all manufacturers of lifting systems to digitalize their information required by their customer, help with HSE, LOLER, ASME and other global legislation compliance to ensure the equipment is not only in good condition, but that it can be inspected prior to being used to carry out a critical lift.

All Kennedy slings are fabricated in ISO 9001:2015 certified facilities, and all hardware is manufactured to exacting standards and meets all safety requirements, the company said.