Where is telematics technology headed?
07 May 2024
Before the year 2000, the term “telemetry” was only associated with NASA and the space program. Today telematics is a mainstream term in the construction equipment industry; telematics technology is constantly evolving through new benefits and new technologies that are being added to those benefits.
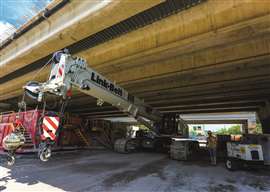
So first, a little history lesson. The term telematics describes the process of long-distance transmission of computer-based information. Telematics components move information from point A to point B. In the case of NASA, telemetry units were sending information from spacecraft and satellites back to Mission Control in Houston. In the case of cranes, wherever they are working, owners have the ability to know everything there is to know about their machines’ operations.
Pertinent data
All crane manufacturers have added telematics hardware to their product lines to monitor everything from simple GPS location to micro-use of a specific component. But even today, the jury is still out regarding the utilization of this data.
Back in 2015, Link-Belt Cranes Vice President Bill Stramer outlined the state of customer use of telematics data at the World Crane & Transport Summit in Amsterdam.
“My experience is that when you ask 10 customers what they want to do with their telematics data, you will get 10 completely different answers,” he said. “As a crane manufacturer, we are in the business of meeting our customer’s expectations through our ‘Voice of the Customer’ quest. But opinions among end users were not at all consistent.”
Today, this sentiment still rings true. Manufacturers tend to harvest data in an aggregate way, not looking at individual machine data unless it is requested by the owner/customer. Manufacturers examine fuel and idle times as well as crane configurations, like use of fly extensions and percentage of lifts completed in specific ranges of chart. These factors aid in their crane design and development for the future and help document the design effectiveness.
At its infancy, what the manufacturers did with the data and true ownership of telematics data was a subject of debate. Today, all manufacturers agree that customers own the data for each crane and they can share as they see fit. To Stramer’s point, some customers share everything with manufacturers and their dealers; others restrict this access and only share when an issue arises.
Standardized data
Beyond ownership of the telematics data, is there a standardization of data that is gathered? In 2016, the Association of Equipment Management Professionals (AEMP), along with assistance from the Association of Equipment Manufacturers (AEM), cooperated to release the AEMP 2.0 Telematics Standard, which also carries an ISO 15143-3 certification. The big point to make here is that the Standard does not include data specific to cranes, and crane OEMs were not included in the Standard. In short, non-crane OEMs agreed to “provide data to the equipment owner in a standardized format for the use and convenience of equipment owners with mixed fleets of equipment.”
But a “crane only” standard is in the works, according to Stephanie Wood, chairman of the AEM Crane Technical Committee. After being approached by the AEMP owners and users of equipment, including cranes, a new ad hoc committee was created to create an ISO standard for telematics for cranes similar to ISO 15143-3 for other construction equipment.
A1A Software Director of Development for Business Applications Brian Burns is a member of the ad hoc committee.
“We are working on a standard like the one for earthmoving equipment that covers crane telematics,” Burns said. “Crane manufacturers are backing the effort and AEM and AEMP are in agreement about what the standard should include.”
Burns is the committee’s only non-manufacturer member, and his technical expertise regarding telematics technology is vital to the roll-out of the standard.
Telematics data points reporting
■ Track location, hours, miles, RPMs and fuel used
■ Breadcrumb tracking to show the path in which your equipment has been
■ Track hours and mileage to determine usage and prepare for maintenance
■ Be alerted to equipment error codes
■ Diagnose problems remotely
Putting it all together
Along with the hardware components installed on cranes by the manufacturer, each brand has its own data collection and viewing portals. Data sent by any telematics unit is cryptic and data intensive. Dashboards have been created to parse the information to something usable for the end-user customer. Today, Link-Belt and Manitowoc/Grove customers use A1A Software portals iCranetrax and CraneStar. Manitowoc has added service portals for Grove and Potain Connect for maintenance plans and predictive maintenance.
Tadano has its original Hello-Net telematics system and has added the IC-1 Remote system that provides cloud-based data views for remote troubleshooting and reduced downtime, according to the company’s website.
Liebherr’s soon-to-be-released “Performance” portal will display real-time crane data and can be accessed through the company’s My Liebherr customer portal.
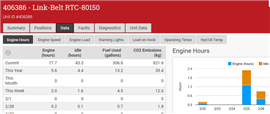
Comansa’s Crane Mate delivers maintenance, location and other necessary data for its tower cranes.
Each portal contains some, or all, of the following data points: odometer, engine hours, idle hours, fuel used, idle fuel consumed, engine service, recent warnings, recent faults, GPS position and crane setup configuration.
Most manufacturers provide their telematic services and access to their dashboard portals for at least two years, without cost to the customer, or while the crane is still under warranty. Customers who see the benefit and use these services and this data can continue past the “free” period as they see fit.
As it was in the beginning, the data is only a benefit if customers use it. Realistically, most users find the location, fuel usage and operational hours the most helpful in determining where and how much their units are utilized. A small percentage of crane owners take advantage of data that helps them with preventative maintenance.
Dash cams
Dual-facing dash cameras are coming to the forefront in the crane industry. At a recent SC&RA transportation event, we found that many insurance companies are providing heavy haul companies with hardware and airtime as part of their annual premiums. Dash cameras are now standard equipment on most over-the-road trucking fleets.
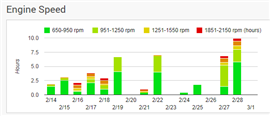
As we have witnessed with other technology, these devices are commonly found on-highway trucks and all-terrain cranes, along with the fleet trucks that support them.
Some self-insured crane groups are now mandated to install the dual-facing cameras by their carriers. In our current litigious environment, dash cameras provide owners a safety net to monitor driving habits of their operators, both good and bad, that can be used in training. Perhaps most importantly, dash cameras capture video with triggers on aggressive driving and, of course, can capture the “truth” in a near-miss or accident.
Insurance savings
With rising insurance rates across the crane industry, the use of these cameras and its reporting, provide significant savings for the crane owner on insurance premiums. They can make nuisance claims go away, with documented video evidence, and help mitigate the “monster” claims when the driver is not at fault.
Today, most dash camera portals are stand-alone for that specific device and don’t integrate with a company’s fleet management or business system. A1A Software has integrated these devices into its iCraneTrax product and continues to deliver the crane customer all the data it needs in one place, including traditional telematics and the new dash cam technology.
THE AUTHORS
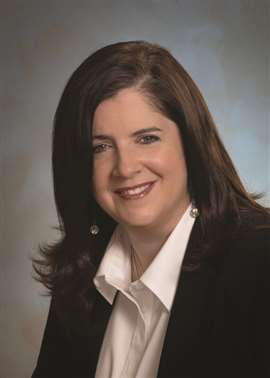
Tawnia Weiss, President and Founder of A1A Software, started the company in 2006. A1A’s flagship product is 3D Lift Plan. In 2012, Weiss and A1A launched iCraneTrax, the company’s crane business management portal, which stores data from every aspect of the crane business into useful information and has a large telematics component.
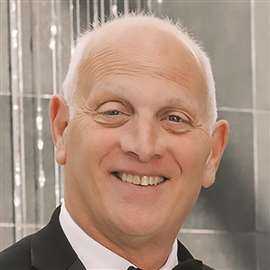
Bruce Kabalen is A1A’s Vice of President of Sales & Marketing since April 2023. Before joining A1A, he spent 25 years as the key technology expert for Link-Belt Cranes. He was the primary liaison with A1A to implement use and acceptance of A1A’s products for Link-Belt’s dealers and customers.